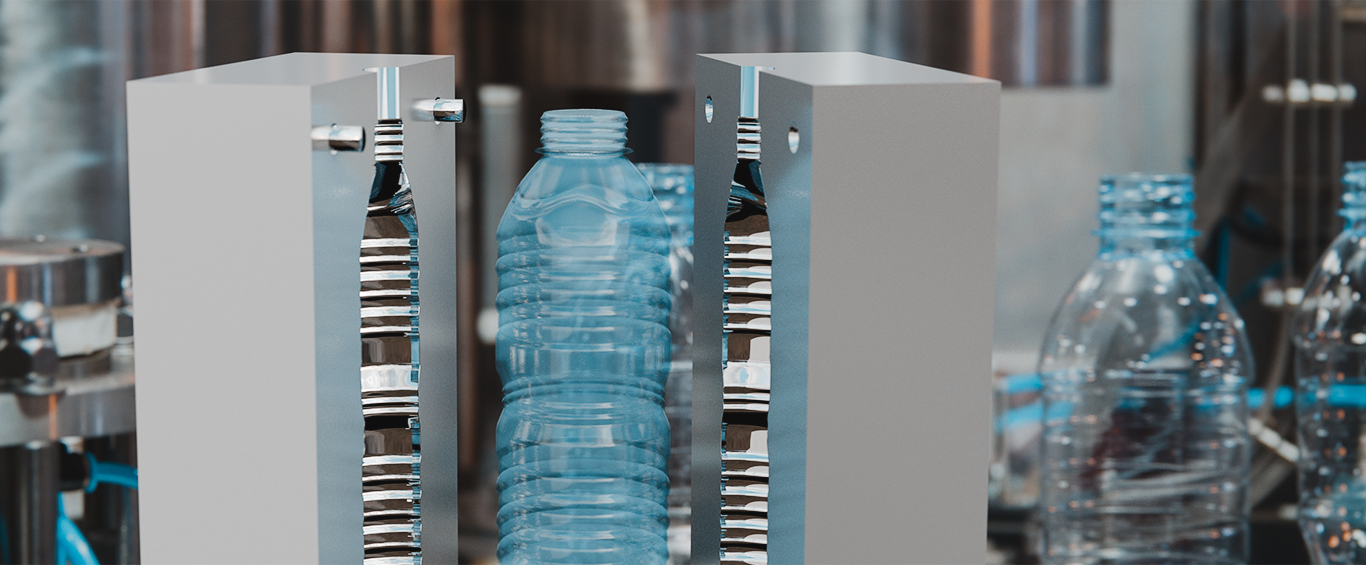
Use case
Extraction of plastic vapours
Extraction of plastic vapours
Perfect extraction and filtering units in extrusion blow moulding technology –
optimum safety for users and equipment
Our engineers – on board from the very start
Engineering begins with the first customer pitch
A leading international company in extrusion blow moulding technology contacted the engineers at Fuchs Umwelttechnik: Complete extraction is required for harmful plastic vapours that occur during the manufacture of hollow plastic products, such as tanks (e.g. IPC), canoes, canisters, bottles or toys.
This extraction unit must be able to collect all emissions efficiently without disturbing the work process.
This extraction unit must be able to collect all emissions efficiently without disturbing the work process.
The initial situation:
In the extrusion blow moulding machine, molten plastic is blown up into its final shape through a nozzle head. The material in this case is polyamide, whereby other types of plastic such as PU can also be used. The machine in XXL format measures 5 m x 5 m x 4 m in height x width x depth and forms a closed system so that no emissions can escape during production.
The task:
Gases and vapours gradually contaminate the inside of the machine and the high-quality technology during operation. When the extrusion blow moulding machine is opened to remove the product after production, the pollutant emissions escape and endanger the health of the staff.
- The emissions contaminate the inside of the machine and the technology.
- The gases and vapours that occur can escape and be inhaled when opening.
Competent expert consulting:
The customer's first contact is already with the engineers of Fuchs Umwelttechnik. The focus here is on sound advice which takes all specific conditions and requirements into consideration. The experts from Fuchs Umwelttechnik develop the requirement specification for the optimum extraction unit together with the customer in the project planning phase.
- In order to find the best solution to the problem, the first talks take place directly between the customer and a specialist engineer from Fuchs Umwelttechnik.
- Project planning: The analysis of all customer requirements as well as the existing working and space conditions are important prerequisites for the tailor-made extraction system.
The solution:
Based on the information acquired from the customer, the engineers at Fuchs Umwelttechnik design the perfectly tailored extraction solution: specifically adapted to the XXL blow moulding machine, the special IFESHKT-06 extraction hood with its specially adapted pollutant capture and efficient transport integrates smoothly into the existing system and guarantees maximum safety.
In detail:
- Complete integration: Mounted underneath the customer's support frame, the special IFESHKT-06 extraction hood fully encases the extrusion station with its three-part, multi-vented extraction unit.
- Complete capture: This arrangement and the special airflow of the extraction unit ensure the capture of all plastic vapours directly at their source.
- Efficient transport: The completely captured emissions on the inside are discharged from the hall with the air current.
- Energy efficiency as a cost saver: The intelligent flow control reduces the energy consumption and therefore sustainably saves running costs.
- Sophisticated design: For safe and easy handling, the special IFESHKT-06 extraction hood is equipped with a practical assembly/disassembly system, PVC strip curtains and a removable cover with magnetic catches and fall protection.
- Made in Germany: The special extraction hood was carefully designed, developed and built at our factory in Steinberg, Germany.
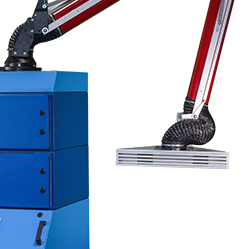
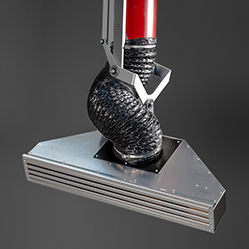
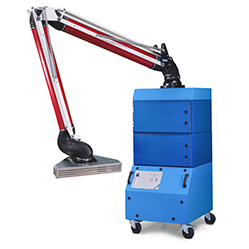
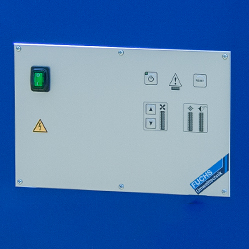
The result:
Fuchs Umwelttechnik supplies this made-to-measure extraction system with technical competence and customer orientation – the special IFESHKT-06 extraction hood. This gives the company in the plastics industry a double lead: On the one hand, this extraction solution gives its staff the safety of clean breathing air and, on the other hand, it prevents contamination of the extrusion blow moulding machine by emissions. In addition, the flow-optimized concept of the extraction unit ensures sustainable and economical operations.